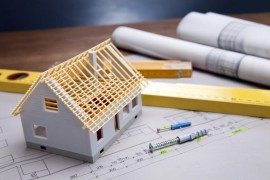
Процесс экструзии поликарбоната и прочие нюансы производства
Среди известных способов переработки поликарбоната выделяется экструзия. Она осуществляется по определенной технологии.
Основные особенности
Экструзией называется процесс продавливания расплавленного сырья через отверстия определенной формы. Немало компаний оказывают услуги экструзии поликарбоната. Материал, характеризующийся пластичностью, прочностью, долговечностью, находит широкое применение для изготовления беседок, навесов, теплиц, заборов, ограждений.
Поликарбонат – продукт химического производства, не перерабатывающийся естественным образом. Его вторичное использование очень важно.
Технология экструзии, применяемая к этому материалу, обладает несколькими преимуществами. Она дает возможность:
- Получить сырье, имеющее правильную структуру, пригодное для производства панелей, вывесок.
- Применять поликарбонат в переработанном виде для изготовления качественных изделий.
Экструзия – оптимальный вариант повторной обработки сырья для получения новых форм материалов. Помимо поликарбоната, ее применяют для реактопластов, эластомеров.
Технологический процесс
Основным устройством, осуществляющим обработку поликарбоната, является экструдер. Конструкция электромеханического прибора состоит из следующих составляющих:
- Нагревающегося корпуса. Достигает температуры, необходимой для расплавки полимеров.
- Рабочего органа. Создает давление, нужное для перемещения материалов. Выполняется в виде поршня, шнека, диска. Наиболее распространен шнековый вариант.
- Фильеры. Такое название получила головка, формующая будущие изделия.
Каждый экструдер оснащается двумя системами:
- Приводной. Сочетает двигатель и редукторную систему. Создает усилие, передает рабочему органу.
- Контролирующей. Поддерживает заданный технологический режим.
Полимерное сырье, попавшее в прибор через узел загрузки, оказывается в рабочей зоне. Там на него воздействует:
- Сила трения.
- Высокое давление.
- Температура.
Нагрев поддерживается на уровне 260-300 градусов, возрастая от загрузочного узла до головки. Шнек давит на расплавленное вещество, заставляя проходить через сетчатые фильтры, формирующие головки.
Затем сырье гомогенизируется, приобретает заданный профиль. Завершающей стадией происходит его охлаждение (принудительным либо естественным методом), полимеризация. На выходе получается высококачественное изделие с запрограммированными механическими, физическими характеристиками.